
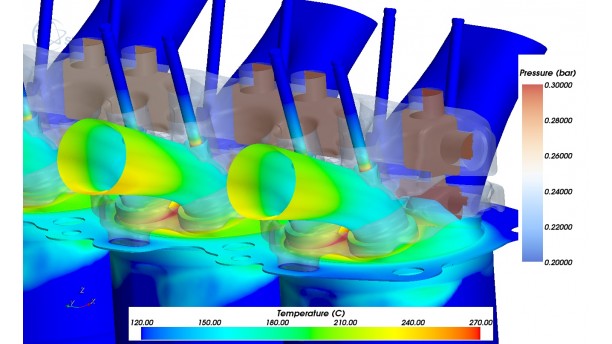
- MODELING NATURAL CONVECTION IN SOLIDWORKS FLOW SIMULATION SERIES
- MODELING NATURAL CONVECTION IN SOLIDWORKS FLOW SIMULATION SIMULATOR
- MODELING NATURAL CONVECTION IN SOLIDWORKS FLOW SIMULATION DOWNLOAD
Designers can apply heat sources, thermal properties on components, and define fan position. With SOLIDWORKS Simulation and/or Flow Simulation, you can simulate structural thermal and fluid flow as well as coupling it with heat transfer, such as convection, conduction or radiation, said Derbal.
MODELING NATURAL CONVECTION IN SOLIDWORKS FLOW SIMULATION SERIES
_Load(Object sender, EventArgs e) in C:\Users\TheWallaces\Documents\Visual Studio 2015\Projects\GoKB\GoKB\:273 SOLIDWORKS offers a series of simulation-in-CAD tools that incorporate thermal analysis. Information regarding the origin and location of the exception can be identified using the exception stack trace below. Please review the stack trace for more information about the error and where it originated in the code.Įxception Details: System.NullReferenceException: Object reference not set to an instance of an object.Īn unhandled exception was generated during the execution of the current web request. Description: An unhandled exception occurred during the execution of the current web request. We were able to run a thermal and fluid flow analysis with SOLIDWORKS Flow Simulation within 24 hours to confirm that the product supplied would work and that the anti-icing would have no hot or cold spots on the separator vanes. Object reference not set to an instance of an object. They issued the order and then came back with some further information on the anti-icing system. The paper presents the effect of the natural convection model on the overcurrent caused thermal runaway simulation results.Object reference not set to an instance of an object. manufacturing problems, operational damages or overcurrent. A typical failure type of OLEDs is thermal runaway caused by e.g. from publication: Development and Characterization of Optimum Heat Sink for 30 W Chip on Board LED Down-Light An optimum.
MODELING NATURAL CONVECTION IN SOLIDWORKS FLOW SIMULATION DOWNLOAD
Steady state and transient simulation results of a free-standing 50 × 50 mm 2 active surface OLED, surrounded by still air, are compared with measurement results. Download Table Material properties used in SolidWorks flow simulation.
MODELING NATURAL CONVECTION IN SOLIDWORKS FLOW SIMULATION SIMULATOR
As a possible workaround to this problem, in this paper the application of five natural convection models for vertical plates in an electro-thermal field solver based OLED simulator as thermal boundary condition are presented. CFD simulation is the obvious way to investigate natural convection environments but integration of a CFD solver in an OLED simulator may be difficult and the solution times are high. Topics covered Heat transfer by conduction Heat transfer by convection Heat transfer by radiation Thermal boundary conditions Analogies between thermal and structural analysis Thermal elements: soli ds and shells Scalar and vector entities, presenting results Steady state thermal analysis Transient. This difference in temperature and current density leads to differential ageing of the organic materials. Thermal Analysis with SOLIDWORKS Simulation 2019 and Flow Simulation 2019 5. In natural convection environment the temperature difference in the same OLED panel can reach 20–30 ☌ which can result in up to 30–40% difference in current density and thus, in the luminance. Despite their lower luminous efficacy their other properties make OLEDs still an attractive option especially in high end indoor applications. OLEDs function as surface light sources and manufacturing of large area light sources is feasible with OLED technologies. Besides classical inorganic LEDs, intelligent light sources can be also based on organic LEDs.
